The installed control system uses a single PLC controller linked to an intelligent closed loop motion controller to synchronize all motors to a ‘virtual axis’. This allows all columns to move, perfectly synchronized, from a single instruction from the PLC.
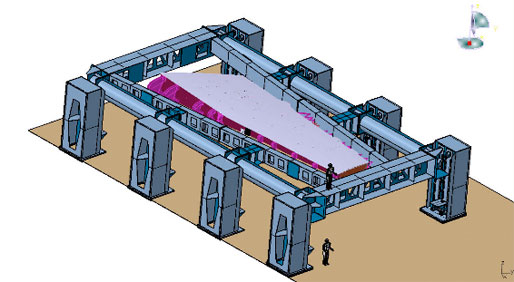
The motion controller is configured to act as if the axis were connected on a mechanical line shaft, known as a ‘Virtual Line Shaft’. The rotation of the ‘Virtual Line Shaft’ causes all eight columns to move precisely. We included in the design built-in backlash algorithms that compensates for gear train losses.
If required any column may be detached from the line shaft using a virtual clutch, and then individually driven.
The associated safety system used is a Siemens Safety PLC with several Profibus connected safety critical devices.
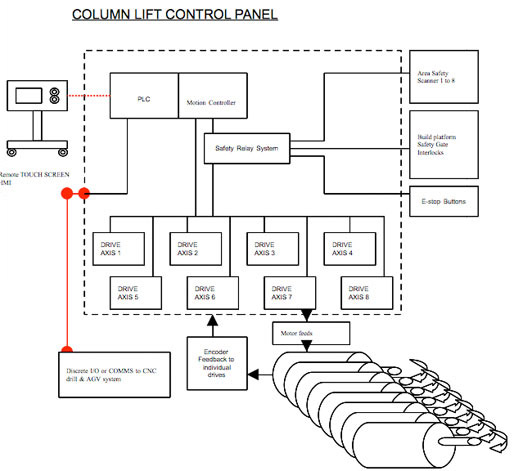
• The PLC / motion controllers selected are form the SIEMENS Simotion series and are basically a combined unit with an architecture platform designed to allow communication with higher level systems and has the following pertinent features.
• Activeline in feed module regenerates into supply removing need for breaking resistors, fully regulated DC bus, this low harmonic solution is particularly suitable for environments with high levels of automation and information systems, it also provides a very compact solution.
•MP377 offers integrated fault diagnostics and easy programming within an a Totally Integrated Automation environment
• Simotion Motion controller provides motion control plus integrated logic functionality.
• ProfiNet communication option included for connection to upstream MIS.
• Modular construction for ease of installation, interconnections via DriveCliQ cables for controller to drives and drives to motors.
• Controller programs and configuration held on memory card, components can easily be swapped without extensive setup or reconfiguration.
• Motors have an electronic name plate, this data is communicated back to the drives by DriveCliQ, this reduces setup and replacement time.
• Simotion has Profibus interface as standard for connection to ET200 remote I/O.
• Siemens Servo motor, 3000 RPM on 400V drive, 26Nm 18A Absolute Encoder With Drive CLiQ Smooth Shaft, With Holding Brake IP 64 Protection, Painted RAL7016, Motor centre height 100 mm
• Single Axis Module 400v 30A, 56A x 250mS 100mm.
• AIMO 400V 80KW 6SL3100-0BE28-0AB0 SINAMI
• FILTER_LINE_3AC_80KW_6SL3000-0BE28-0DA0
• Active Line Module 400V 80 kW 300mm (includes fan cooler)
• SINAMICS S120 Compact Flash Card, firmware + P1 licence, with Performance 1 Extensions CBE30 Profinet Communications Card
• Simotion D435 (Requires 512MB CF & Multi-Axis RT
• CU320 SINAMICS CONTROL MODULE w/o Firmware
|